Using the PWM Driver Wildcard
The PWM Driver Wildcard contains eight MOSFET PWM (Pulse Width Modulation) low-side drivers which convert logic-level PWM outputs to the high current drive required of solenoids, actuators, heaters, coils, lamps, control valves, motors and other devices.
The PWM Driver Wildcard does not create PWM signals itself, but converts logic-level PWM signals into high-current capability. It connects directly to the field headers on Mosaic's PDQ Board to be driven by the logic-level PWM outputs of the PDQ Board's 9S12/HCS12 MCU, and optionally provides current monitoring using the processor's built-in analog to digital converter (ADC). However, you can also use this board as a high-current PWM amplifier/driver or solid-state switch array for PIC and Arduino microcontrollers as described here.
The PWM Driver Wildcard is ideal for instrumentation of large load devices which do not provide their own "variable" control. It allows interfacing the 9S12/HCS12 MCU's PWM outputs to high current loads.
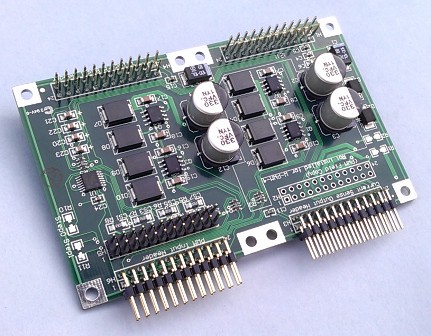
PWM output specifications
The PWM Driver Wildcard provides the following key functions:
- 8 channels of up to 5 A current each with field voltages to 26 V
- One or two independent field voltages, each powering 4 channels
- Fast PWM switching, <0.5 μsec turn ON/OFF times
- 4 channels of current sensing with user-configurable gain
- Field connections to a standard 24-pin header or to solder holes
- 5A per channel at low PWM frequencies, 3.4 A total for each set of 4 channels for high frequency PWM
Its output channels have the following electrical specifications:
High Current DC Outputs (each channel, without heat sink, TA = 0 to 70 °C) | |
---|---|
Output Channels: | 8 open-drain current sinking outputs at up to 5 A each (limited to user-configured current-sensing full scale) |
MOSFET Used: | DMG4800LSD 30V 7A N-MOSFET |
Output Protection: | Snub diodes to field supplies to protect against inductive spikes |
Field Voltage: | +4 to +26 VDC max for two field supplies, each driving 4 channels |
Current measurement: | Current measurement outputs for four channels with full scale configurable to 172 mA, 860 mA or 4.3 A |
OFF Voltage: | +4 to +26 V (field supply) |
OFF Leakage: | < 1 μA at 25 °C |
ON Voltage: | 0.016 V at 1 A continuously, 0.08 V at 5 A, for channels without current measurement |
Max ON Resistance: | <0.022 Ω for channels without current measurement, 0.04 to 0.52 Ω for current measurement channels |
Max ON Current: | 5 A continuously each channel alone, current full scale for current measurement channels |
Switching Times: | ton = 0.12 μsec, toff = 0.2 μsec for 10%-90% transitions |
Weight: | 46 gram for 8-channel version, 42 gram for 4-channel version |
Size: | 4" x 2.5" x 0.5" 1) (50.8mm x 63.5mm x 12.7mm) |
A logic high (5VDC) placed on one of the inputs (PP0-PP7) turns on its corresponding output. You can use two different field supplies, designated VA+ and VB+, if you need to control devices that require different voltages. Each of the PWM Driver's channels provides a MOSFET switch to turn ON/OFF current into your controlled device. Figure 1 is a simplified schematic2):
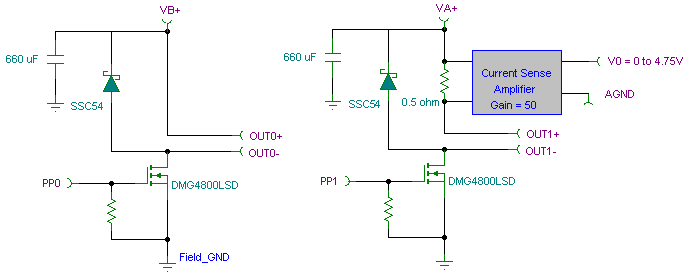
The field supplies and current settings are apportioned among the channels as shown in the following table:
Channel | Field Supply | PWM Clocks | Current Sensing Output3) | ||
---|---|---|---|---|---|
Out 0 | – | VB+ | CLOCKA / SA | – | (no current sensing) |
Out 1 | VA+ | – | CLOCKA / SA | – | V0=0-4.3 V for 0-172 mA FS |
Out 2 | – | VB+ | – | CLOCKB / SB | (no current sensing) |
Out 3 | VA+ | – | – | CLOCKB / SB | V1=0-4.3 V for 0-172 mA FS |
Out 4 | – | VB+ | CLOCKA / SA | – | (no current sensing) |
Out 5 | VA+ | – | CLOCKA / SA | – | V2=0-4.3 V for 0-860 mA FS |
Out 6 | – | VB+ | – | CLOCKB / SB | (no current sensing) |
Out 7 | VA+ | – | – | CLOCKB / SB | V3=0-4.3 V for 0-4.3 A FS |
For variations from these specifications for first article boards see Customizations of first article boards below.
Connecting to the PWM inputs and outputs
The PWM Driver Wildcard is 4"x2.5" (102x64mm) in size – twice the size of most other Wildcards, and making it the same size as the PDQ Board. You can mount it on the PDQ Board, connecting its Digital Input and Analog Output headers through short ribbon cables to corresponding headers on the PDQ Board below. Its two Wildcard Bus Headers pass the Wildcard bus up through the board so that you can mount other Wildcards on top of it.
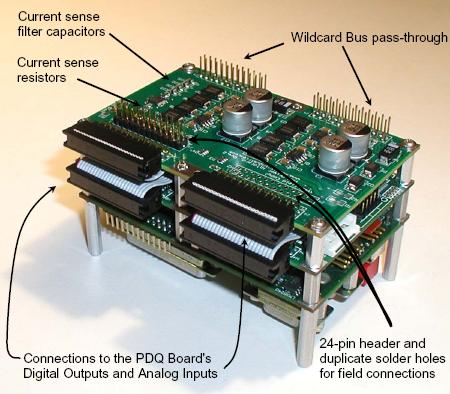
The above photo shows a PWM Driver Wildcard mounted on a PDQ Board, which in turn is mounted on a Docking Panel. The PWM Driver is connected to the PDQ Board through short ribbon cables for its PWM input signals and current sensing voltage outputs. Field connections are made to the 24-pin vertical header, or to mirrored copies of those signals appearing at a 24-hole pattern on the board. The Wildcard Bus stacking connectors are provided so that you may mount other Wildcards over the PWM Driver Wildcard. The Wildcard bus is not otherwise used.
Making your input connections
The Wildcard is controlled by eight logic-level signals placed on its Input Header, H6. These control signals are internally pulled down so if you do not connect to an input its corresponding output is turned OFF. Normally you would use a short ribbon cable to connect H6 to the PDQ Board's Digital Output Header, H8, allowing the PDQ Board's PWM outputs to be used. Be sure to include the connection of pin 1, the ground pin. If you are driving the board from another microcontroller or other logic signals, you should follow the pin-out of the following table.
While you should use the ground pin, pin 1, there is another, essential ground connection that must also be made. In order to turn on the board's MOSFETs the input logic signals are compared to the field ground. Consequently, the PDQ Board ground must be connected to the field ground, FIELD_GND, at a single point somewhere within your instrument, and preferably close to the connection between the PDQ Board and the PWM Wildcard. As a fail-safe and protective measure, the ground of pin 1 is connected to the FIELD_GND through back-to-back diodes on the board, but you should not rely on that connection alone. Proper grounding is shown in the circuit diagram below.
H6 – Input Header | |||
---|---|---|---|
Signal | Pins | Signal | |
GND | – 1 | 2 – | |
– 3 | 4 – | ||
– 5 | 6 – | ||
– 7 | 8 – | ||
PP7 | – 9 | 10 – | PP6 |
PP5 | – 11 | 12 – | PP4 |
PP3 | – 13 | 14 – | PP2 |
PP1 | – 15 | 16 – | PP0 |
– 17 | 18 – | ||
– 19 | 20 – | ||
– 21 | 22 – | ||
PT1 (may be connected to PP2) | – 23 | 24 – | PT0 (may be connected to PP0) |
Note: 1. You normally connect this header to the PDQ Board's Digital I/O Header, H8. Connecting to other ports requires a custom ribbon cable. 2. You must also connect the field supply ground to the PWM Wildcard's ground (pin 1) or the PDQ Board ground near the board. 3. For using pins PT0 and PT1 for feedback control, see counting-pwm-pulses. |
Field connections to the high current PWM outputs
Connections to the devices you want to control and to their field power supply are made to the board's Field Header, H5. The header provides straight 0.025" pins to which you can connect a standard IDC (ribbon cable) socket. The header is mirrored by a set of empty holes on the board, designated H2. You can connect to those holes by directly soldering wires to them. The following signals appear on the pins of the two headers:
H2 & H5 – Output Field Header | |||
---|---|---|---|
Signal | Pins | Signal | |
Field_GND | – 1 | 2 – | VA+ |
Field_GND | – 3 | 4 – | VA+ |
Out_0– | – 5 | 6 – | Out_0+ |
Out_1– | – 7 | 8 – | Out_1+ |
Out_2– | – 9 | 10 – | Out_2+ |
Out_3– | – 11 | 12 – | Out_3+ |
Out_4– | – 13 | 14 – | Out_4+ |
Out_5– | – 15 | 16 – | Out_5+ |
Out_6– | – 17 | 18 – | Out_6+ |
Out_7– | – 19 | 20 – | Out_7+ |
Field_GND | – 21 | 22 – | VB+ |
Field_GND | – 23 | 24 – | VB+ |
Note:VA+ is used to power outputs 1, 3, 5, and 7 and VB+ powers outputs 0, 2, 4, and 6. |
To power channels 1, 3, 5, and 7 you must provide field power and ground to pins 2 & 4 (VA+) and pins 1 & 3 (Field_GND) respectively. You should make power and ground connection to both sets of pins, to minimize connector contact resistance. Likewise, to power channels 0, 2, 4, and 6 you must provide field power and ground to pins 22 & 24 (VB+) and pins 21 & 23 (Field_GND).
Separate power inputs are provided for the odd and even numbered channels so that you may use different field supply voltages for them. If all your channels require only a single field voltage, you may connect the VA+ and VB+ pins together, and supply your field voltage to all four pins to minimize connector contact resistance. You may also connect the supplies together on the board by installing a zero ohm short at location R2, but it is still a good idea to minimize the source resistance of the power supply connections by connecting to all four power input pins, 2, 4, 22, and 24. The ground lines on pins 1, 3, 21, and 23 should all be used to return the current to the negative side of your field supply.
Each output appears on the connector as a set of pins, one to source current (Outn+) and the other to sink it (Outn-). If you are using high frequency PWM control, you may need to connect your device through a shielded twisted pair cable to minimize radiated noise.
If you are using low frequencies, or merely turning ON/OFF devices, you may not need twisted pairs, and can use standard ribbon cable. Standard ribbon cable connectors are specified at 1 amp per connection. If your loads require more current, consider using Mosaic's higher current ribbon cable and connector, part number IDC24-26AWG-24IN. Using that, you can switch as much as 4.5 A rms using a single, isolated line (with all of the ground wires connected together to carry the return current), or up to 1.5 A rms using all eight outputs simultaneously. See the discussion of ribbon cable and IDC socket current handling capability at Ribbon Cable Current Rating.
Connecting with shielded twisted pair cable
With respect to the cables you use, you have some choice depending on the magnitude of current you expect to drive:
- Standard 0.050" (1.27mm) wire separation, AWG 28 (7/36 stranded) gauge ribbon cable for connection to IDC sockets can handle up to 1 A current for short runs. It has a resistance of 200-250 mΩ/m (61-76 mΩ/ft).4) The IDC socket/header connection provides a contact resistance of 10-15 mΩ maximum.5) See Ribbon Cable Current Rating for detailed specifications for ribbon cables of differing current capabilities.
- Standard size shielded twisted pair cables are available from several manufacturers. The Belden specifications chapter of their product catalog is a good source of basic information on the current handling capacity of such cables. Belden PN 1325A and 1326A two and three pair cables provided shielded twisted pairs with recommended current capacity of 2.6 A (and max current capacity of 5 A for short runs) per pair.6)
The following table provides data for several exemplar shielded twisted pair cables:
Belden PN | Pairs | Gauge | Resistance | Current 7) |
---|---|---|---|---|
1327A 1328A | 2 pair 5 pair | 18 AWG (7x26 stranded) | 19.2 mΩ/m (5.9 mΩ/ft) | 5A - 8A |
8762 | 1 pair | 20 AWG (7x28 stranded) | 31 mΩ/m (9.5 mΩ/ft) | 3.9 A - 6.5 A |
1266A 1269A 1325A 1326A | 1 pair 2 pair 2 pair 3 pair | 22 AWG (7x30 stranded) | 48 mΩ/m (14.7 mΩ/ft) | 2.6 A - 5 A |
Note that 20 and 22 AWG stranded wire will fit into the holes on the Wildcard, but 18 AWG is a little too large, so a few strands would need to be trimmed before soldering. |
Connecting to the current sense outputs
If you require the use of the current sense outputs, a ribbon cable is used to connect the Current Sense Output Header, H3, to the PDQ Board Analog Input Header, H4. Power for the current sense circuitry is taken from the PDQ Board through this header (pins 1 and 2), and four output voltages are provided on pins 21-24. These correspond to the first four 10-bit resolution analog inputs on the PDQ Board. The output voltage level for all channels is 4.75V. No connections are made to the other pins.
H3 – Current Sense Output Header | |||
---|---|---|---|
Signal | Pins | Signal | |
AGND | – 1 | 2 – | +5VAN |
– 3 | 4 – | ||
– 5 | 6 – | ||
– 7 | 8 – | ||
– 9 | 10 – | ||
– 11 | 12 – | ||
– 13 | 14 – | ||
– 15 | 16 – | ||
– 17 | 18 – | ||
– 19 | 20 – | ||
(for Out_7) V3 | – 21 | 22 – | V2 (for Out_5) |
(for Out_3) V1 | – 23 | 24 – | V0 (for Out_1) |
Note:V0-V3 are 0-4.75V outputs corresponding to channel currents. You normally connect this header to the PDQ Board's Analog I/O Header, H4. Connecting to other ports requires a custom ribbon cable. In that case, the cable must supply +5VAN and AGND power signals. |
If you need 16-bit current resolution, the Wildcard's current-sense voltage outputs can be connected to the Analog I/O Wildcard instead of the PDQ Board's Analog I/O header. In that case, a custom cable must be fabricated following the pin-outs of the above table.
If you are using the PWM Driver Wildcard stand-alone, you may use a voltmeter or other measuring device to measure the voltage outputs at the pins of the above table.
Signal polarity
A logic level high at the PWM output of the PDQ Board causes a channel of the PWM Driver Wildcard to turn ON, which turns ON its open-drain output transistor, which produces a LOW voltage on its output pin, OUT-. The load (your device like a heater or control valve) is connected between the output, OUT-, and the positive terminal of your field supply, OUT+ (or in the case of the current sensing channels, through a small current sense resistor to the positive field supply). The low output voltage on OUT- turns ON your device causing current to flow. So there is a voltage inversion – when your device is ON, the voltage at the OUT- is LOW.
Counting PWM pulses
Two of the PWM input signals on the PWM Input Header may be looped back to the PDQ Board's timer input pins so that as PWM pulses are produced they may simultaneously be counted. That capability is useful when the PWM Driver Wildcard is used to drive stepper motors. PWM signal PP0 may be connected to input capture signal PT0 by installing a 1kΩ resistor at location R10, and PP1 may similarly be connected to PT1 by installing a 1kΩ resistor at location R11.
Dynamic performance
The PWM outputs do not switch instantaneously, but require a little time to turn ON and OFF, ultimately limiting the maximum frequency of operation. Further, there are slight differences in turn ON and turn OFF delays, resulting in a small error in the duty cycle produced. In general, you can switch high currents efficiently and accurately at frequencies up to 100 KHz. At that frequency the duty cycle error is of the order of 1%. (It is less than 0.1% at 10 KHz.)
For more information, consult this detailed analysis of the PWM output switching delays and slew rate.
Preventing noise radiation from PWM signals
High frequency, high current PWM signals are notorious for radiating noise – EMI or electromagnetic interference. Consequently it's essential that if you use PWM currents to control internal or external devices, you must wire connections to those devices in a way that minimizes radiated noise. In general, single point grounding and the use of shielded twisted pair cable are essential to preventing EMI, as detailed in Preventing PWM Noise.
Setting the current measurement range
For four of the eight channels, that is, channels 1, 3, 5, & 7, you can monitor the drive current. The voltage across a current sense resistor is amplified by a factor of 50, averaged with a time constant of 10 msec, and presented as an output voltage in the range 0-4.3 V. The output voltage is measured by the PDQ Board's 0-5 V A/D inputs.
The current is averaged throughout the entire PWM period so that both the ON and the OFF currents are accounted for. The output always indicates the time-weighted average of the ON and OFF currents. For resistive loads the current is a square wave, with full current during the ON time and zero current during the OFF time. That square wave current profile is averaged, and presented as an output voltage with a small, triangular ripple current. For inductive loads the inductor's current continues to flow during the OFF time so that the current waveform is a triangular wave. It is averaged to produce a DC output with only a very small, nearly sine-wave ripple voltage.
Although the board is usually shipped with default resistor values for the current sense resistors, you can replace the sense resistors to change the scale of current measurement. The resistors are located near the edge of the board. They are surface mount devices in 1206 packages; the packages were chosen large enough to allow easy replacement and resoldering. The resistor designators for each channel are as follows:
Designation | Channel | Default value | FS Current |
---|---|---|---|
R8 / CS1 | Out_1 | 0.500 ohm | 172 mA |
R7 / CS3 | Out_3 | 0.500 ohm | 172 mA |
R6 / CS5 | Out_5 | 0.100 ohm | 860 mA |
R5 / CS7 | Out_7 | 0.020 ohm | 4.3 A |
To change a channel's full scale current range, simply unsolder the appropriate resistor and replace it with one chosen from the following table, which shows the current range provided by various common 0.1% tolerance resistor values:8)
Current Range | Resistor Value | Resistor PN | Output Voltage Range |
---|---|---|---|
0 – 4.300 A | 0.020 ohm | CSR1206FK20L0 | 0 – 4.3 V |
0 – 1.720 A | 0.050 ohm | CSR1206FK50L0 | 0 – 4.3 V |
0 – 0.860 A | 0.100 ohm | CSR1206FKR100 | 0 – 4.3 V |
0 – 0.430 A | 0.200 ohm | CSR1206FKR200 | 0 – 4.3 V |
0 – 0.172 A | 0.500 ohm | CSR1206FKR500 | 0 – 4.3 V |
0 – 0.086 A | 1.00 ohm | CSR1206FK1R00 | 0 – 4.3 V |
The current measurement accuracy as a full scale (FS) gain error is typically ±0.6% FS (±2.6% max) at 25 °C, and ±5.6% over temperature (-40 °C to +125 °C). The zero or offset error is typically ±0.6% FS.
Setting the current filter time
The current sensing outputs are filtered by a single pole RC filter with a default time constant, τ, of 10 msec. You can change the filter time constant by soldering in different values for the filter capacitor.
Designation | PWM Channel | Output | Default Value | Default Filter Time |
---|---|---|---|---|
C21 | 1 | V0 | 10 μF | 10 msec |
C22 | 3 | V1 | 10 μF | 10 msec |
C20 | 5 | V2 | 10 μF | 10 msec |
C23 | 7 | V3 | 10 μF | 10 msec |
The filter time constant scales with the value of the installed capacitors. For example, 0.1 μF provides a τ = 0.1 msec time constant, while 100 μF would provide a 100 msec time constant. If you change the PWM duty cycle frequently and need faster responsiveness for the current measurement you would choose a shorter time constant. On the other hand, if you want the greatest measurement accuracy you would choose a greater time constant.
The worst case ripple on the output voltage as a portion of full scale is,
You can choose a capacitor value to keep the ripple below a design specification. For example, if you need the ripple to be less than ±0.5%FS, you need the time constant, τ, to be greater than,
The following table provides sample values of capacitor to use if you want to customize the board:
Ripple | PWM Frequency | Minimum τ | Capacitor to use |
---|---|---|---|
± 0.5% FS | 20 kHz | 1.25 msec | 1 μF or greater |
± 0.5% FS | 5 kHz | 5 msec | 10 μF or greater |
± 0.5% FS | 1 kHz | 25 msec | 22 μF or greater |
± 0.1% FS | 20 kHz | 6.25 msec | 10 μF or greater |
± 0.1% FS | 5 kHz | 25 msec | 22 μF or greater |
± 0.1% FS | 1 kHz | 125 msec | 100 μF or greater |
Note that these values assume worst case conditions in which a resistive load is being driven. For inductive loads, the load itself filters the current, then the RC filter further reduces the ripple. Consequently, the ripple voltage is very much less than that calculated above.
If your load is inductive with a great enough inductance to operate in continuous current mode with a triangular shaped waveform, then the ripple current is reduced by another factor of,
where the inductive filtering time constant, L/r, is determined by the load's inductance, L, and internal resistance, r 9).
Drive current capability
Current capability differs between current-sensing channels and non-current-sensing channels. The channels equipped with current sensing capability provide a maximum current limited by their current sensing resistor. For standard boards those current limits are;
Channel | Full Scale Current |
---|---|
Out 1 | 172 mA |
Out 3 | 172 mA |
Out 5 | 860 mA |
Out 7 | 4.3 A |
You may change the full scale currents by changing the values of current sensing resistors, as described in Setting the current measurement range.
For the non-current-sensing channels, there are three factors that limit the current handling capability of each channel:
- The board's connectors are rated to carry a maximum of 1 A. You may exceed that while testing briefly, but you can not rely on the connector's sustained ability to safely carry greater currents. You can bypass this limitation by soldering directly to the board;
- The switching MOSFET transistors and flyback diodes have maximum current specifications which affect the steady state and dynamic current capability of individual channels – limiting each channel to a maximum of 5A; and,
- The onboard power filtering capacitors have a maximum ripple current limitation that affects the current capability of the two sets of four channels. Each set of four channels is limited to 3.4 A at high PWM frequencies. You can supply much greater currents when using lower frequencies, or you can add external capacitors to allow greater currents.
You must stay within the maximum limits of each of these sets of components. As these limits sometime depend on the number of channels used and the PWM frequency and duty cycle, they are discussed in more detail below.
Connector current capability
Standard ribbon cable connections and wires are rated for 1 A per connection, but we have available special ribbon cables and sockets with 2 A per conductor capability. For greater current and to reduce noise radiation, you should use shielded twisted pair cable.
Use a socket of sufficient current rating
The field header on the PWM Driver Wildcard is rated for continuous currents up to 2 amps per pin and it should mate with a socket that is capable of carrying the required load current for your application. Note that standard insulation-displacement ribbon cable sockets are rated at only 1 amp of continuous current per contact. If you need more current, choose a ribbon cable and IDC cable socket capable of the current, for example Mosaic's part number IDC24-26AWG-24IN, and read the discussion of ribbon cable current capability.
Directly solder to the board
If you use shielded twisted pair cables, and solder the wires directly to the board using header H2, you can control greater currents. You may choose a cable capable of 5 A continuously from the table above of Belden cable part numbers.
Steady-state current capability of individual channels
The MOSFET and diode components for each output channel are rated to handle 5 A of continuous current in the steady state, that is, at 100% duty cycle. You can gang several channels together, and drive them together, to provide even greater current to external devices. However, we do not recommend that as it makes it more difficult to stay within the limitations of the other factors discussed here. in particular, the standard connectors do not withstand currents greater than 2 A.
Dynamic current capability of individual channels
At duty cycles less than 100%, you can sink proportionally greater currents per channel, so long as the average current is kept to 5 A. If you need to provide brief, infrequent high current pulses you will need to consult the datasheets for the MOSFET and flyback diode to see what the maximum current is as a function of pulse duration and frequency.
Dynamic current capability of sets of channels
Onboard capacitors filter the field power supply voltages for each set of four channels. VA+ and VB+ are each filtered by 660 μF of capacitance. The filter capacitors are provided to prevent high current pulses from radiating from the supply lines and to reduce the effect of power supply source impedance, both inductive and resistive, on the voltage provided to the load devices.
A disadvantage of providing onboard filter capacitors is that you must stay within their ripple current limitations. The ripple current flowing through the capacitor's equivalent series resistance (Resr) produces power that must be dissipated by the capacitor package. At low PWM frequencies that poses little problem – ripple current is only produced when the PWM output changes, and at low frequencies the transitions are infrequent and the ripple current is small. But at high PWM frequencies appreciable ripple current is produced in the filter capacitors. In addition to frequency, another factor that must be considered is the source impedance of the field power supply. If its source impedance is low, it provides the current needed, and the filter capacitors' ripple current is low. But if the source impedance is appreciable, more demand is placed on the capacitors to provide the necessary PWM current.
The result of these considerations is that at high PWM frequencies the ripple current limitation of the capacitors limits the combined current you can provide from each set of four channels.
The worst case occurs when all four channels synchronously pulse at 50% duty cycle. In that case, the combined maximum current you can provide for a set of four channels is given by the following equations:10)
For fPWM < 1/(4τ)
and for fPWM > 1/(4τ)
where
Rs = Power supply source resistance for VA+ or VB+
Resr = Capacitor esr = 0.038 Ω at 10 kHz, 0.05 Ω at 1 kHz, 0.1 Ω at 100 Hz.
C = Filter capacitance = 660 μF
τ = (Rs+Resr) C, and,
fPWM = PWM frequency
For the worst case conditions of high PWM frequency, 50% duty cycle, and high power supply source impedance the combined currents of the four channels are limited to twice the allowed ripple current, or 3.4 A,
For more realistic conditions, suppose Rs = 0.15 Ω (0.1Ω for the ESR of the power supply output capacitors and 0.05 Ω cable resistance), then the critical frequency is,
For PWM frequencies above this,
But for significantly lower PWM frequencies, for example 100 Hz,
At these frequencies, each of the four channels could simultaneously use its full 5 A without creating too much capacitor ripple current.
Gaining greater dynamic current capability
The above computations assumed a worst case scenario of several high current PWM outputs operating synchronously, all at 50% duty cycle. However, if your outputs are asynchronous and at other duty cycles you will be able to support more current. There are several other ways to optimize the current handling capability of the board:
- If you have two high current outputs you should use one of channels 0-3 for one output and one of channels 4-7 for the other. That way, each channel will get its full worst-case 3.4 A maximum current.
- If you have several high current channels for which you must sense their currents you are constrained to place them on channels 0-3 so that you can measure their current. In that case, if you do not need a separate supply for the other set of channels (4-7) you should connect the VA+ and VB+ supplies either externally, or on-board by placing a zero ohm short at position R2, or both, and deliver your field power to both sets of power pins. By doing that you combine the filter capacitance for the two sets of channels, and now have a worst case maximum current capability of 6.8 A.
By soldering larger filter capacitors to the board you can gain a greater dynamic current capability. For example, if you are using a 12 V field supply and you have space available above or below the board, you can solder a large radial leaded 16V capacitor to the extra holes for the VA+/FIELD_GND or VB+/FIELD_GND connections. If that capacitor has a lower ESR than those onboard, it will provide most of the ripple current.
A suitable capacitor may be PN EKY-160ELL822MMP1S, an 8200 μF, 16V capacitor with 0.014 Ω ESR and 4.22 A ripple current capability. That capacitor will boost one set of four channel's maximum current capability to approximately 11 A.
A similar, high ripple current capacitor to use with field voltages up to 24 V is PN EKZE350ELL182ML25S, a 35 V, 1800 μF, 0.016 Ω ESR, 3.46 A ripple current capacitor. Its use would boost the current capability of a set of four channels to about 10 A.
- The lower the source impedance of the field supply, the less demand is made on the onboard filter capacitors. Consequently, following the above equations, you can boost the board's current capability by placing the field supply close to the board, using heavy cables for connection, and soldering the cables directly to the board.
Using the Wildcard separately or with PIC microcontrollers
You can use the Wildcard without connecting it to a PDQ Board or other Mosaic controller if you wish. You can connect it to the output of other microcontrollers, as described in Using PWM Driver with Other Microcontrollers.
PWM circuit schematic and datasheets
Customizations of first article boards
( 4 τ fPWM )^(1/2) *
(1-exp[-1/2τfPWM]) (1-exp[-1/τfPWM])^(-1/2)Owing to the exponentials, this equation shows two behaviors, with a rather sharp transition between the two regimes.
For (4τfPWM) < 1 the above can be approximated as,