Designing Step-Down (Buck) Switching Regulators
How to choose inductor and capacitor values
There are many switching regulator integrated circuits available that perform most of the functions you need to build step-down regulators. For example, the LM2678, LM22678 and TPS5450 switching regulator ICs are low cost and highly effective power supply building blocks. To use them, you need to know how to design and specify a few other circuit components, most importantly input capacitors and output inductors and capacitors. The IC datasheets are often very informative, but they also often do not include the fundamental information you need to make informed trade-offs among component specifications. This design guide is intended to provide the fundamental understanding needed to make those design decisions so that you can specify components with confidence.
A buck regulator configuration provides a ground referenced output voltage using the circuit schematic shown in Figure 1. The regulator comprises a high-side switch controlled by an integrated circuit, a flyback diode (sometimes augmented with a low-side switch as shown in the schematic), and an LC filter. Some regulator ICs incorporate the high-side switch while many other do not. Also, ICs may or may not include a synchronous rectifier, or the drive capability for an external synchronous rectifier.
The high-side switch produces a square wave by switching the input of the LC filter between roughly the input voltage and ground. The LC filter smooths that switching waveform, removing its AC component, and producing an average DC output voltage. The controller circuit within the IC samples the input and output voltage, compares the output voltage to a reference, and uses the error to vary the duty cycle, d, of the high side switch with the aim of producing a constant output voltage. That output voltage is delivered to a load, Rload in the schematic, which consumes an average current, Iload = Vout/Rload.
The duty cycle of the high-side switch, always between 0 and 1, is the ratio of its ON time to the total period of the switching waveform.
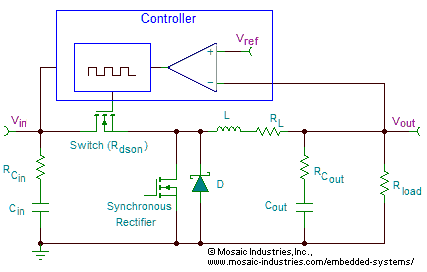
The various resistors in the circuit represent the equivalent series resistance (ESR) of each component:
RL is the ESR of the inductor, and,
RCout is the ESR of the output capacitor.
Figure 2 shows a typical example of such a circuit using the LM2678 Buck Switching Regulator.
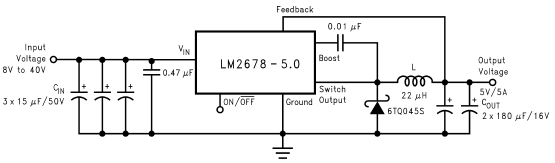
Circuit operation
Most buck regulator controllers use a fixed frequency, and vary only the duty cycle of the waveform to produce the output voltage. Some are able to turn up the duty cycle to unity or turn it down all the way to zero, while others limit at a maximum and minimum duty cycle. For those that limit at a minimum duty cycle, depending on the controller, lesser output voltages may be produced by pulse skipping or lowering the switching frequency.
In the circuit of Figure 1, when the high-side switch is ON, the voltage presented to the LC filter is the input voltage less the small voltage drop across the switch. Little power is dissipated in the high-side switch; when ON there is only a small voltage drop, and when OFF there is no current. When the high-side switch turns OFF, the diode turns ON and the inductor current continues. The voltage at the input of the LC filter is now -VD, the voltage drop across the diode. To minimize that voltage, and the power loss it causes, some designs include an optional low-side MOSFET switch which acts as a synchronous rectifier. The voltage across the low-side switch when it is ON is generally much less than a diode drop, so the power loss is greatly reduced.
Regulator design is done assuming that the regulator will spend most of its time in continuous current mode, in which current continuously flows through the inductor. When the high side switch is ON, the current in the inductor increases, storing energy in the inductance while also supplying current to the load; when the high side switch is OFF, the inductor current decreases, while the inductor continues to supply current to the load. The output capacitor buffers the current variation so that the load sees a nearly constant output voltage.
Output voltage
When operating in continuous current mode, the output of the regulator, Vout, is nearly directly proportional to the duty cycle, d, roughly as,
This equation shows the beauty of the buck regulator configuration – it is inherently stable, with the voltage output simply proportional to the input and the duty cycle. It is therefore easy to control; to maintain a constant output, the controller only needs to compensate for input voltage variations and second-order effects resulting from varying load current. Even a simple open-loop controller that produces a duty cycle inversely proportional to the input voltage can work well.
The above equation does ignore the second-order subtleties such as switching and inductor resistance and diode drop. A more complete model considers those factors, showing the output voltage as a duty-cycle-weighted average of the switching waveform, minus several IR drops, like this,
where,
I is the average current in the load resistor,
RDSON is the ON resistance of the MOSFET switch,
VD is the ON voltage of the flyback diode, appx. 0.5 V, and,
RL is the equivalent series resistance of the inductor L.
Inductor ripple current
Assuming that the switching frequency, F, is well above the LC filter's cut-off frequency, in continuous current mode the inductor current is a triangular waveform. We can find the peak-to-peak ripple current, Ipp, by recognizing that during the ON or OFF time of the waveform the change in inductor current is proportional to the voltage across the inductor as V = L ΔI/ΔT. Using this relationship, the peak-to-peak ripple current in the inductor is given by,
⇒ Ipp = ( Vin - I RDSON - Vout - IrL ) ( d/ F ) / L
⇒ Ipp = d (1-d) ( Vin - I RDSON + VD ) / (L F)
∴ Ipp ≈ d (1-d) Vin / (L F)
This ripple current is maximum at 50% duty cycle (where Vout ≈ Vin /2), and is given by,
Continuous vs discontinuous current mode
There is a minimum load current necessary to preserve a continuous current through the inductor. That current is one half of the peak-to-peak inductor ripple current. So long as the load current is greater than that value, the inductor current continues throughout the entire PWM waveform. In that case, the output voltage is simply proportional to the product of the duty cycle and the input voltage, as shown in Equation 11). Regulator operation is said to be in continuous current mode.
However, if the load current falls below that level, the inductor current drops to zero at some point during the OFF time of the high side switch, and the regulator is then said to be in discontinuous current mode. In that case, the output voltage rises above that predicted by Equation 1, and becomes sensitive to the absolute level of output current. If no output current is drawn from the regulator the output voltage will rise as high as the input voltage for any duty cycle greater than zero (d > 0).
- Iload > Ipp / 2 ⇒ continuous current mode.
- Iload < Ipp / 2 ⇒ discontinuous current mode.
Or, in greater detail,
- Iload > Vout ( 1 - Vout / Vin) / (2 L F) ⇒ continuous current mode.
- Iload < Vout ( 1 - Vout / Vin) / (2 L F) ⇒ discontinuous current mode.
While in continuous mode the output voltage depends primarily on the input voltage and duty cycle (as shown in Eqn. 1, in discontinuous mode it also depends on the output current and the absolute ON time (or operating frequency), as shown in the following equation.
If we can neglect VD (as it's small compared to Vout), we can rewrite the above equation more analogously to Eqn. 1, as,
Here we see that for a fixed operating frequency and duty cycle, when we draw no current from the regulator if the duty cycle is anything greater than zero the output voltage rises to the input voltage. As we draw current the output voltage steadily decreases until the regulator enters continuous mode, after which the the output voltage stabilizes, becoming largely independent of the current, and follows Eqn. 1.
Operating frequency and filter cut-off frequency
Most modern IC step-down switching regulators use a fixed frequency of operation. For example, the LM2678 uses 260 KHz while the LM22678 and TPS5450 both use 500 KHz.
Integrated circuit buck regulators such as these contain a control circuit block that modulates the duty cycle to provide constant output voltage. The control is relatively easy as the circuit produces an output voltage directly proportional to duty cycle and input voltage, minus some IR drops. The controller measures the input voltage and uses feed forward control to compensate the output for changes in input voltage. It then samples the output voltage, compares it to an internal reference, and modulates the duty cycle to compensate for load variations.
The control system is stable so long as the output filter cut-off frequency is not too large. In general, to assure stability, the closed-loop unity gain bandwidth (also called the closed loop cross-over frequency on some datasheets) should be limited to one-sixth or less of the switching frequency. The unity gain bandwidth is the frequency at which the loss of the LC filter becomes greater than the internal gain of the controller. This requirement places a minimum on the value of the output capacitor. You'll need to consult the datasheet of the IC regulator you are using to determine the constraints on output capacitor value. In general, for a regulator with a switching frequency in the range of 100-500 KHz the filter's low pass cut-off frequency, that is,
should be in the range 1-25 KHz.
How to specify the inductor
Properties important for inductor selection are its inductance (L) its equivalent series resistance (RL), its maximum current carrying capability (Imax), and its saturation current (Isat). There is a trade-off among these properties. In general, a large inductance will reduce the output voltage ripple but at the cost of slowing down the regulator's transient response and increasing the inductor power loss by virtue of its increased ESR. On the other hand, a small inductance will improve the transient response and reduce its power loss but increase the output voltage ripple and risk the inductor's being driven into saturation.
We'll discuss each of these critical properties in turn.
Inductance
The minimum required inductance is determined from the allowable ripple current. Generally, in continuous current mode the peak-to-peak ripple current, Ipp, should be kept to less than 30% of the average current, I. That is, from Equation 4,
For example, for input voltages up to 28 V and a maximum output current of 5 A, at a switching frequency of 500 KHz the inductance must be greater than 9.33 μH. At a switching frequency of 260 KHz the inductance must be greater than 18 μH.
At greater frequency, or if we were to decrease the maximum allowed voltage, we could use a proportionally smaller inductors. A larger inductor can be used, which by virtue of its lesser ripple current eases requirements on capacitor selection, but its maximum value is subject to size, weight, and ESR limitations.
Some inductors are rated on their datasheets in terms of their E⋅T product, rather than their inductance×current product. In this case, the required E⋅T is given by,
or
E⋅T = d (1-d) Vin / F
You can see from Equation 7 that the worst case requirement, where E⋅T is maximum, occurs when d = ½, in which case Equation 7 is really a restatement of Equation 6, but cast in terms of E⋅T rather than in terms of L and Ipp. It is useful for assessing those inductors whose datasheet use E⋅T ratings.
Inductor ESR and maximum current
Power dissipation within the inductor depends on its equivalent series resistance and the RMS current through it. The RMS current is given by,
where the RMS value of the triangular ripple current is given by the peak-to-peak value divided by 2√3.
The maximum RMS current the inductor can sustain is determined by its ESR, RL, and its allowable temperature rise. It power dissipation of I2rms RL raises its temperature to a degree determined by its thermal resistance to ambient. The temperature rise has two drawbacks. First, as the core heats up it generally loses inductance. Consequently, when considering the rating of the inductor you should use the worst case inductance at the greatest anticipated operating temperature, not necessarily at 25 °C. Secondly, the insulation on the wires within the inductor will eventually fail. So you must keep the current less than that which could cause failure at the greatest ambient temperature.
Further, you must take into account that for board mounted inductors heat will be transmitted to nearby components, significantly raising their ambient temperature.
Saturation inductance
At high currents the inductor's core eventually saturates so that its marginal (or small-signal) inductance decreases to zero. On datasheets, the saturation current is usually defined as that current at which the total inductance (not the small signal inductance) decreases by 20% or 50% of its low current value. Operating an inductor above the saturation current causes rapidly increasing core losses. Further, driving an inductor deep into saturation results in runaway switching current, and can destroy the regulator's high-side switch.
When specifying an inductor you should assure that the peak current, where,
is less than the saturation current so as to minimize core losses. Further, the inductance at the maximum current must be greater than the minimum inductance needed to keep the ripple current below its chosen value.
Specifying the output capacitor
There are four considerations to choosing the output capacitor: the filter cutoff frequency, the maximum allowed output ripple voltage (which depends on the capacitance and its ESR), and the capacitor's sustainable ripple current and working voltage ratings. We'll discuss each in turn.
Filter cutoff frequency
The regulator chip's internal control system is stable so long as the output filter's low-pass cut-off frequency is low enough. If the filter cut-off frequency is too great the regulator risks instability, if it is too small the regulator is slow in responding to variations in load. It is better to err on the side of a low frequency, and hence a larger filter capacitor.
The closed-loop unity gain bandwidth (aka closed loop cross-over frequency) should be no greater than one-sixth of the switching frequency. The closed-loop unity gain bandwidth is the frequency at which the high frequency loss of the LC filter is greater than the controller's internal gain. Most IC controllers do not publish their internal gain in an understandable form on their datasheet, but they do often provide guidance in choosing the output filter's cut-off frequency. For example, the datasheet of the LM22678 (which operates at 500 KHz) specifies that the filter cut-off frequency should be limited to the range of 1.5 - 15 KHz. You can compute the filter's low pass cut-off frequency, fc, from Equation 5.
Another way to look at the LC components is as a filter which smooths the square wave at its input into a DC voltage at its output plus a small ripple voltage. The attenuation of this 2nd order filter is proportional to the square of the operating frequency (for sine waveforms). Consequently,
or,
fc/ F = √(Vpp/Vin)
where,
ω = 2πF and fc ≡ 1 (2π √(LC))
In this view, the capacitor should be chosen to make the filter cut-off frequency low enough for the output ripple to be minimized. For example, if the output ripple is to be only 0.5% of the input voltage, the ratio of filter cutoff frequency to operating frequency should be 1/√200, at the most. For the 500 KHz LM22678 the filter cutoff frequency would then be smaller than 35 KHz. Some regulators, the LM22678 included, may require an even lower cutoff frequency to assure stability of the regulator's internal control loop. A more detailed analysis that considers the capacitor ESR and a factor to compensate for the square wave shape of the input waveform is presented below in eqn15.
Output ripple voltage
The output capacitor's function is to buffer the varying inductor current so that it causes a minimal ripple on the output voltage. The output ripple voltage is produced by two components, reactive and resistive, with a 90° phase difference.
The first, or reactive component, Vpp-C, is produced by the varying current in the capacitance, and is computed from the fundamental formula for capacitance, ΔQ=CΔV, by,
The second, or resistive component, Vpp-R, is computed as,
The pythagorean sum of these two components is the total output ripple voltage:
Substituting the value of ripple current caused by a particular inductor choice (from Equation 4) into Equation 13 produces,
Or, if the capacitor's ESR is negligible,
We can see from Equations 14 and 15 that the output ripple as a portion of the supply voltage is proportional to the 1/LC. For the ripple to be small, both the resistive and reactive components of the capacitor's impedance must be sufficiently small.
To follow our example, for,
L = 15 μH,
F = 500 KHz, and, Vpp < 0.1 V
the total capacitor impedance must be less than,
To obtain a capacitor ESR or the order of 0.1 Ω or better usually requires employing the best of aluminum electrolytic capacitors. The capacitance must be greater than,
If we use a capacitance that is much greater than this value, so that the capacitive reactance is much small than the capacitor's ESR, then only the ESR makes a significant contribution to the output ripple voltage. So, for example, we could use a capacitance of 47 μF and require the ESR to be below 0.1 Ω.
Using greater output capacitance has the advantage of buffering load transients so that less demand is placed on the regulator's feedback controller. However, greater capacitance often comes with greater bulk, expense, and ESR, which results in greater output ripple voltage. In general, there's a sweet spot in capacitor value, where the capacitance is great enough that the output ripple voltage is determined primarily by its ESR (and not its capacitive impedance), but the ESR is not too great.
Ripple voltage is further decreased by operating at lower input voltages, using a larger inductance, or by paralleling multiple identical capacitors for lower overall ESR.
RMS current rating
The output capacitor absorbs the inductor's varying current, that is its ripple current, to provide a nearly constant Vout. The ripple current waveform is roughly triangular – its RMS value is the peak-to-peak current divided by 2√3. Consequently, the output capacitor must have a sufficient RMS current rating, given by,
Working voltage rating
The voltage rating of the output capacitor should be about 30% greater than the maximum input supply voltage. Even for a step-down regulator with fixed output voltage, in the event of failure of regulation the output voltage may rise to the input voltage. Consequently, to avoid catastrophic failure of the output capacitor it should be rated to withstand the input voltage. For example, for Vin up to 27V you we use a capacitor rating of 35 V. You must also consider the power dissipation in the capacitor, so the capacitor voltage rating must be de-Rated to less than the nominal room temperature rating.
Specifying the input capacitor
When the high-side switch turns ON, the load current is drawn from the input supply. You can't count on the impedance of that supply to be able to supply the current pulse, so an input capacitor smooths the current drawn from the input and provides the square wave pulses of current the regulator needs.
RMS current rating
The input capacitor's ripple current is
It is maximum when d = ½, that is, when the output voltage is one half the input voltage. In that case, it is,
Input capacitor ripple voltage
The input capacitor ripple voltage comprises two components, a reactive triangular component, and resistive square wave component, which sum to a peak-to-peak magnitude of,
Again, this is maximum when the output voltage is one half of the input, or d = ½,
Working voltage rating
Like the output capacitor, the voltage rating of the input capacitor should be about 30% greater than the maximum supply voltage, and de-Rated appropriately for elevated temperature.
Specifying the flyback diode
The diode must be specified to handle the required voltage, current, and power.
- Voltage rating: When the high-side MOSFET switch is ON, the diode is reversed biased by the input voltage. You should choose a reverse voltage rating at least 30% greater than the maximum input voltage.
- Current rating: When the high-side MOSFET switch turns ON, the current through the inductor continues to flow, but it now flows through the diode, forward biasing it. The average diode current is ( 1 - d ) I. You should choose a diode that can handle the worst case load current at the expected duty cycle.
- Power rating: The overall efficiency of the switching supply is degraded by the power lost in the diode. To minimize that power, you should minimize the forward bias voltage by using a Schottky diode. Make sure that the power rating of the diode is greater than the expected average power, ( 1 - d ) I VD, and that its temperature rise is not too great.
Regulator limitations
Many IC regulators, for example the TPS5450 or LM22678, have minimum controllable switch ON and OFF times. Consequently they have minimum and maximum duty cycles and minimum and maximum output voltages. For some regulators, driving its feedback pin high will cause it to produce the minimum duty cycle, while others will produce lower duty cycles despite their minimum ON times by skipping pulses. The minimum output voltage consequent to a minimum duty cycle is,
Most IC switching regulators set their output voltage by comparing an internal reference voltage to a voltage derived from the output through a voltage divider network. Consequently, they can produce an output voltage in value greater or equal to their internal reference. Even so, you can use an op-amp circuit to actively drive the feedback pin to attain lesser output voltages.
Regulator efficiency
The average current drawn from Vin is,
and the average input power is,
where d is the duty cycle and I is the load current.
The major sources of power loss, which impact the overall efficiency of the circuit, are identified in the following table. These formulas provide estimates for power dissipation when the regulator is operating under continuous conduction mode. They are not applicable for light loads in the discontinuous conduction mode.
Circuit component | Power loss | Comments |
---|---|---|
Flyback diode | I VD ( 1-d ) | This loss may be minimized by using a Schottky diode or a synchronous rectifier |
Inductor | 1.1 I2RMS RL | The additional 10% is added as an approximation of core loss. |
High side switch | d I2RMS RDSON | |
Switching loss | 0.01 Iload Vin | |
Output capacitor | I2RMS-Cout RCout | IRMS-Cout is the capacitor RMS ripple current. |
Quiescent current loss | Iquiescent Vin | |
Input capacitor | I2RMS-Cin RCin | IRMS-Cin is the capacitor RMS ripple current. |
If these power losses are summed, the worst case efficiency of the regulator can be easily estimated.
See also →